CNC Tool Holder:CNC Lathe Tool Holder Types Uses Benefits
XY-GLOBAL specialises in CNC shank types, using our expertise to keep up with the latest machining technology. With a wide range of shank types to choose from, it is important to review your options and decide on the type of shank that best suits your needs.
A tool holder is a machining component that holds the end mill in place. Its purpose is to hold the tool in place as precisely and firmly as possible, as a barely perceptible increase in runout can ruin your project or break your cutting tool.
Different types of holders have varying levels of runout and balance. There is also variation in their lifespans and durability. Another important factor to consider when picking a CNC tool holder is the time it takes to change end mills, as it directly impacts your bottom line.
What Is a CNC Tool Holder?
The spindle of your CNC machine operates the cutting tool and controls the precision process. However, interference is required to prevent damage to your spindle and cutting tool. A tool holder provides the necessary margin between these two components.
CNC tool holders are designed to safely hold a cutting tool in a precise location. Depending on the tool holder you choose, some offer incomparable accuracy and a firm grip, while others allow the cutting tool to float to prevent a broken tool.
All holders need to be precision-engineered to offer the cutting accuracy and long-lasting performance you need. A damaged tool holder can be a major setback and costly replacement, so it’s important to invest in the right holder and look for signs of wear.
A precision tool holder can keep your CNC machine turning out excellent workpieces of all types. Work with a tool holder manufacturer who can help you get the most out of your CNC machine. Versatile equipment deserves versatile accessories and tooling.
- ●Shrink fit holders : This type of holder uses heating and cooling to apply clamping force to the cutting tool. Shrink fit holders offer powerful grip and can dramatically extend tool life.
- ●Collet chucks: A collet chuck grips the end mill with a slotted collar. Standard collets are sized by millimeter, and they can be customized as well.
- ●End mill holders:These parts use a set screw to secure the cutting tool. They have small nose diameters and are available in a variety of lengths.
- ●Pull Stud Series :The spigots are manufactured from the best steel to ensure minimal wear and guarantee a strong core that is resistant to the normal wear and tear caused by CNC machines.
Quality Product
All of our products are made from high-quality materials and designed to increase the lifespan of your tools and save you time and money. Contact XY-GLOBAL to learn how our standard and customized tool holders can improve your operation
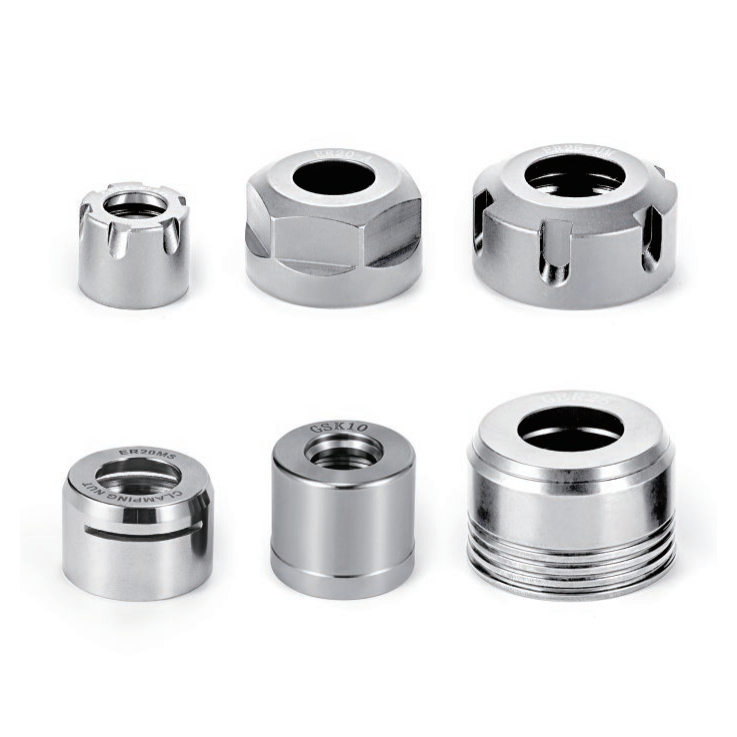
Proper Tool Holder Maintenance
A tool holder, if maintained, can handle high-performance CNC machining day in and day out. However, a tool holder undergoes extreme pressure with heavy use. Over time, this vital component will need to be serviced or replaced.
The most important maintenance step is a thorough inspection and cleaning. Routinely disassemble and clean your tool holders to prevent contamination, corrosion and other issues. The exact timeline can vary, depending on your holder and the amount of use it receives.
Collets can be replaced every two to three months if they are used continuously throughout the day. A worn collet will cause your tooling to wander, which affects the quality of your production and the life of your cutting tool.
If you have any questions about the life of your tooling, work with a leading manufacturer. Discuss any signs of reduced performance and ask about the ideal maintenance routine to keep your CNC machine operating efficiently.
Choosing the Right Toolholder for Your Needs
Selecting the appropriate toolholder is crucial for efficient machining. Small and large companies rely on factors like machine type, process, and product. Shorter tool holders are preferred to reduce vibration and damage from chatter and imbalance. However, for deep insertions, longer tool holders are essential.
Taper spindle type varies. BT-type suits small, high-speed work, while HSK toolholders are for high-precision, high-speed tasks.
Consider insertion depth, quick tool changes, and cut specifications when choosing. Consistency in the final product aligns with industry and customer expectations. Toolholders not only ensure safe cutting processes but also extend machine life.
In conclusion, the right toolholder choice balances factors for optimal performance, enhancing productivity and quality. With years of experience and a team of reliable engineers, XY-Global offers customized toolholders to cater to your specific requirements. Visit XY-Global online to explore our catalog and inquire about which type of toolholder suits your needs.