Temperature requirements for alloy die casting parts
The alloy die casting process has relatively high requirements for the temperature control of the mold, and the temperature of the mold is a key factor in the heat dissipation of the metal solution, the filling of the mold and the solidification process of the casting. In many cases, abnormal mold temperatures can cause casting defects. The use temperature can reach as high as 350 °C, which can meet the temperature requirements of aluminum alloy, magnesium alloy, zinc alloy and other alloy die-casting.
Alloy die casting generally has a higher temperature. In order to meet the required mold temperature, the traditional process usually uses a petroleum gas gun or plug-in heating tube to heat the mold, and the mold temperature is uneven and the effect is not good. We all know that in the die-casting process, the alloy solution enters the mold cavity through pressure, and the heat loss solidifies and molds to obtain the die-casting. The temperature control of the mold plays a key role in die casting production. If the heat loss is too fast, die casting will produce cold lines, slow heat dissipation, increase die casting molding time, and reduce productivity. Therefore, mold temperature control refers to the mold heating and maintaining at a certain working temperature to ensure the stable quality of the casting, shorten the compression cycle, and extend the service life of the mold.
The ideal method is to heat the mold with a die-casting mold. Using the high heat transfer and fluidity of the heat transfer oil, the mold is indirectly heated by the heated heat transfer oil to bring the mold to the desired temperature.
If you have precision die casting parts for the semiconductor, medical and optical field, please send the drawing inquiry to us for further evaluation.Our Email: sales820@xy-global.com
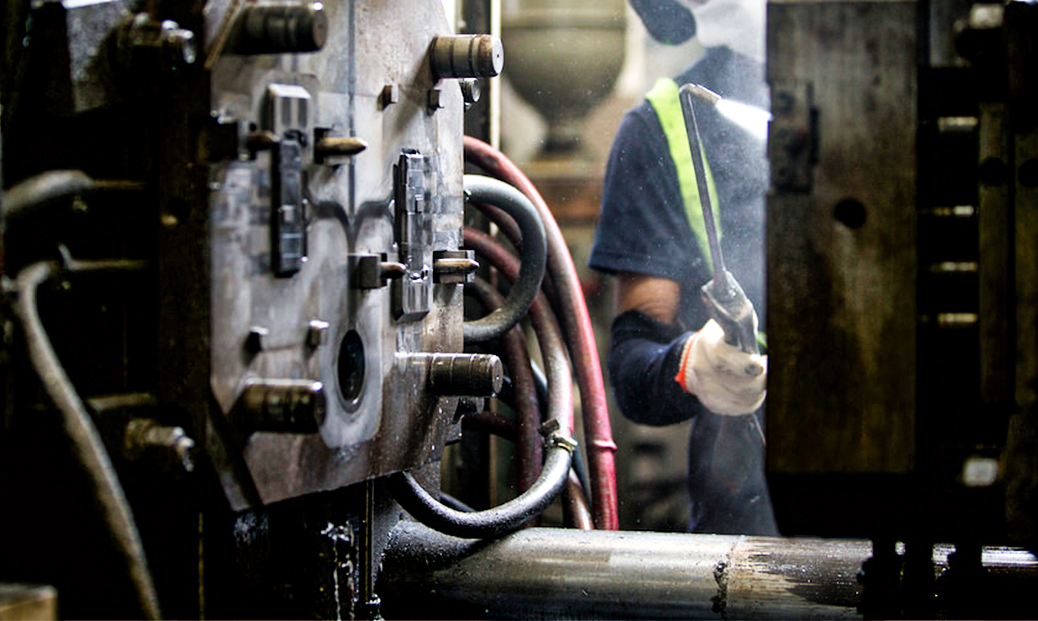