Zinc alloy grinding and polishing method
Before the zinc alloy die-casting parts are polished, the workpieces with serious cracks, air bubbles, shrinkage holes and loose parts can be removed before they can be polished and polished.
Grinding is mainly to remove the surface burrs, parting lines, flashes and other die casting defects of the workpiece to obtain a roughly flat and smooth surface. Grinding adopts cloth wheel, the diameter of the cloth wheel is 50~400mm, the maximum peripheral speed shall not be greater than 2500m/min, and the small parts use the low speed of 1100~1400m/min. The adhesive abrasive on the cloth wheel is 0.069-0.045mm, and the sharp angle should be chamfered. The main polishing paste is iron oxide as the polishing auxiliary material, and dry grinding is not allowed. Grinding should be carried out in one direction, the grinding marks should not cross, and the grinding pressure should not be too large to avoid excessive grinding.
The polished workpiece can be polished, and the polished workpiece should reach Ra0.025~0.05μm. Polishing should be done with a cloth wheel, non-stick abrasive, first rough with red polishing paste, and then finely polished with white polishing paste (alumina). Use less polishing paste when it is more shiny. , to avoid difficulty in degreasing due to excessive polishing paste. However, if the polishing paste is not used or the polishing paste is too small, the surface of the part will be overheated locally, resulting in pitting, and bubbles are easily generated during electroplating. The speed of the polishing wheel should not be greater than 2150m/min, and the small parts should be 1100-1600m/min. When polishing, the pressure should not be too high, pay attention to the amount of grinding, polishing should be carried out in one direction, and the grinding marks should not cross. After the polished parts are inspected, they should be placed in special workpiece tools to prevent scratches. Polished parts should be processed as soon as possible, otherwise the aged polishing paste will be difficult to handle.
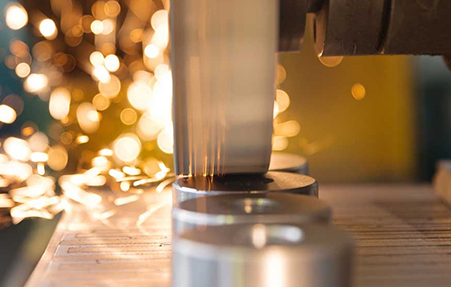